Ergonomics Analysis
Has your facility received an Ergonomics Analysis?
If so, How long has it been since your last evaluation?
Ergonomics Analysis
Has your facility received an Ergonomics Analysis?
If so, How long has it been since your last evaluation?
Workplace Ergonomics Analysis
Workplace conditions are in constant flux. Work processes can change, new products or job functions are introduced, and employees needs can change. Smart companies schedule a periodic Ergonomics Analysis to ensure compliance, reduce workplace injuries, and keep production at a top-performing level. At McClure Ergonomics Consulting, we recommend an analysis every one to five years, depending on your facility and your industry.
The McClure Ergonomics Consulting Employment Testing is both 100% ADA and EEOC compliant without discrimination toward gender, age or disability. During your facility review, we look at several factors that can affect worker’s health, safety, and productivity.
- Workplace conditions
- Workstation design
- Work practices
- Workflow
- Production process
- Risk factors
- Injury records
- Workers’ compensation claims
- And more
In addition to our analysis, we may conduct a workplace survey and/or speak to individual employees about their job functions. We take the time to identify existing issues that will need to be adjusted or changed. Many times, we find issues that have either gone unnoticed or resulted from a facility change. These issues, if left unchecked, can result in future injury claims as well as lost productivity. These common proactive methods serve as best practices to identify any existing risks or prevent future risks in the workplace.
Importance of an Ergonomics Analysis
Do you have staff members who are working at a slower pace, acting uncomfortable or are experiencing pain? The physical and mental health of your employees–whether working from the office or working remotely–is essential to your business success. It is in every business’ best interests to maintain a healthy and productive workforce. These outward behaviors can be a sign of ergonomic problems in the work place.
Your first step should be to talk with your workers. When you take the time to listen, they will feel understood and valuable to the organization. Find out what issues they are facing and how they would like to improve their job functions and work environment.
Your next step is to call us! McClure Ergonomics Consulting will work onsite to conduct research and identify problems within your work space. We’ll pinpoint existing problems as well as catch other issues before they occur.
Ergonomics Analysis Tools
At McClure Ergonomics Consulting, we use a variety of science-based, industry-approved tools to ensure the most accurate results for our clients. Through an evidenced-based approach, we are able to recommend measurable improvements to your workplace conditions. By ensuring that all job tasks fall within workers’ capabilities and limitations, we help our customers optimize both performance and production.
Our customers put our trust in us so that their businesses remain fully functional and safe for all employees. That’s why we go above and beyond to deliver top-notch, evidence-based results that keeps your bottom line in mind.
McClure Ergonomics Consultants uses the following scientific ergonomics analysis tools that meet American National Standards Institute (ANSI) standards. These tools will identify, quantify, and reduce ergonomic risk factors within your company.
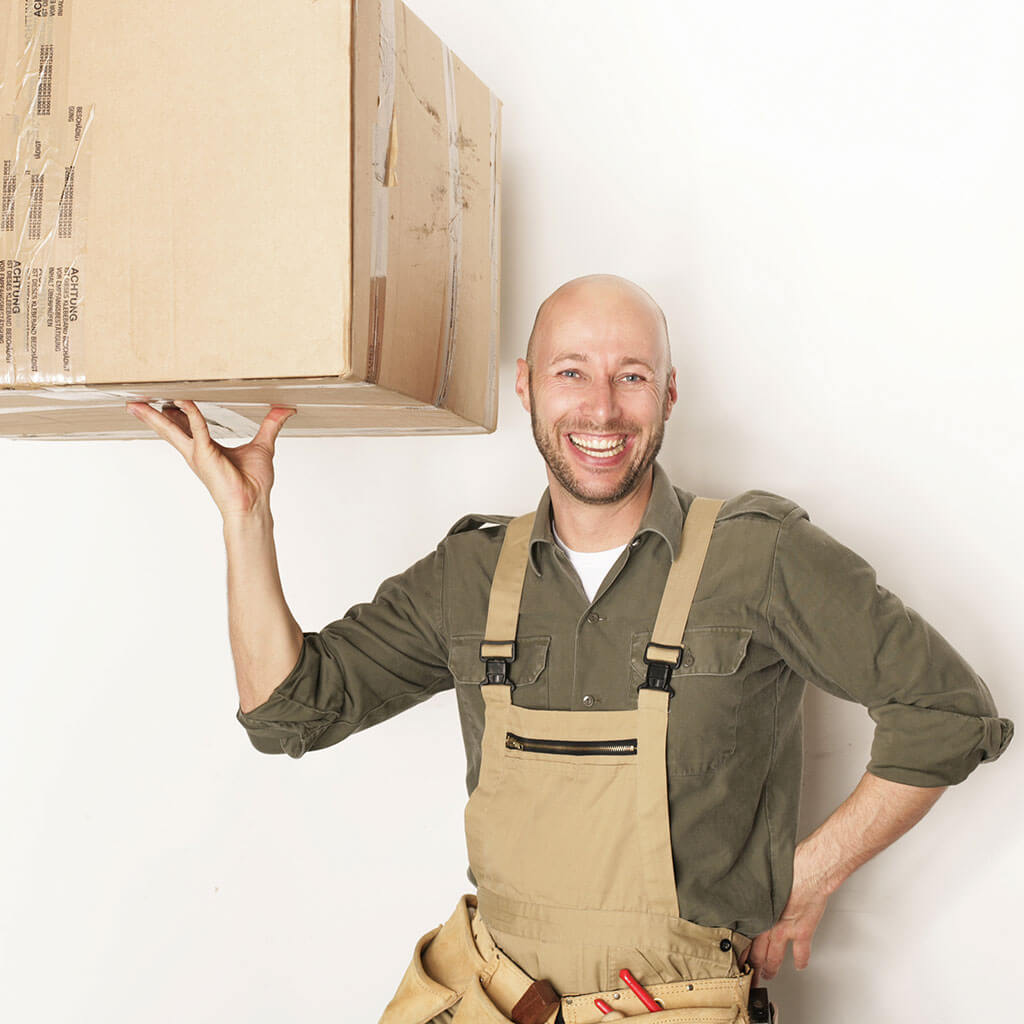
NIOSH Lifting Equation
The NIOSH Lifting Equation is a tool used to assess the risks involved with lifting and lowering tasks within the workplace environment. By analyzing manual material handling functions, we are better able to determine safer lifting and lowering practices and guidelines to avoid both injury and overexertion.
Through the NIOSH lifting equation, we can determine the Recommended Weight Limit (RWL), which is the maximum appropriate weight load that most healthy employees can lift over the course of an 8-hour day without increasing the threat of developing any musculoskeletal disorders (MSD) to the spine and lower back.
In addition, NIOSH also provides a Lifting Index (LI), which is an estimate of MSD risk as well as a determination of the level of physical stress related to any manual lifting tasks.
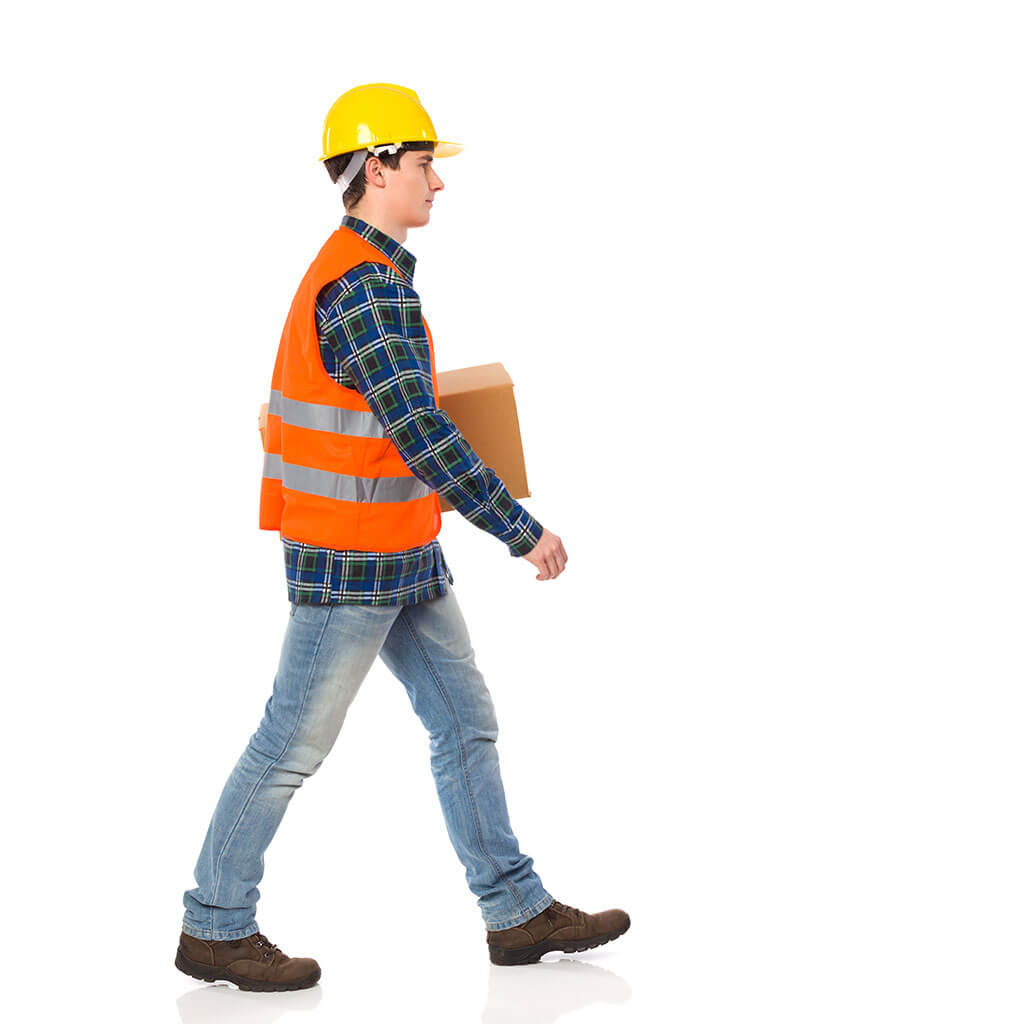
Rapid Entire Body Assessment (REBA)
The Rapid Entire Body Assessment (REBA) scientifically assesses whole body posture, movements and actions, forceful exertions, repetitive movements, and coupling as they relate to job function. This tool also evaluates MSD risk and any ergonomic risks connected with job tasks.
The following body regions are evaluated through a REBA.
- Wrists
- Forearms
- Elbows
- Shoulders
- Neck
- Trunk
- Back
- Legs
- Knees
Your evaluation will consist of a single score that represents the MSD risk for each part of the body.
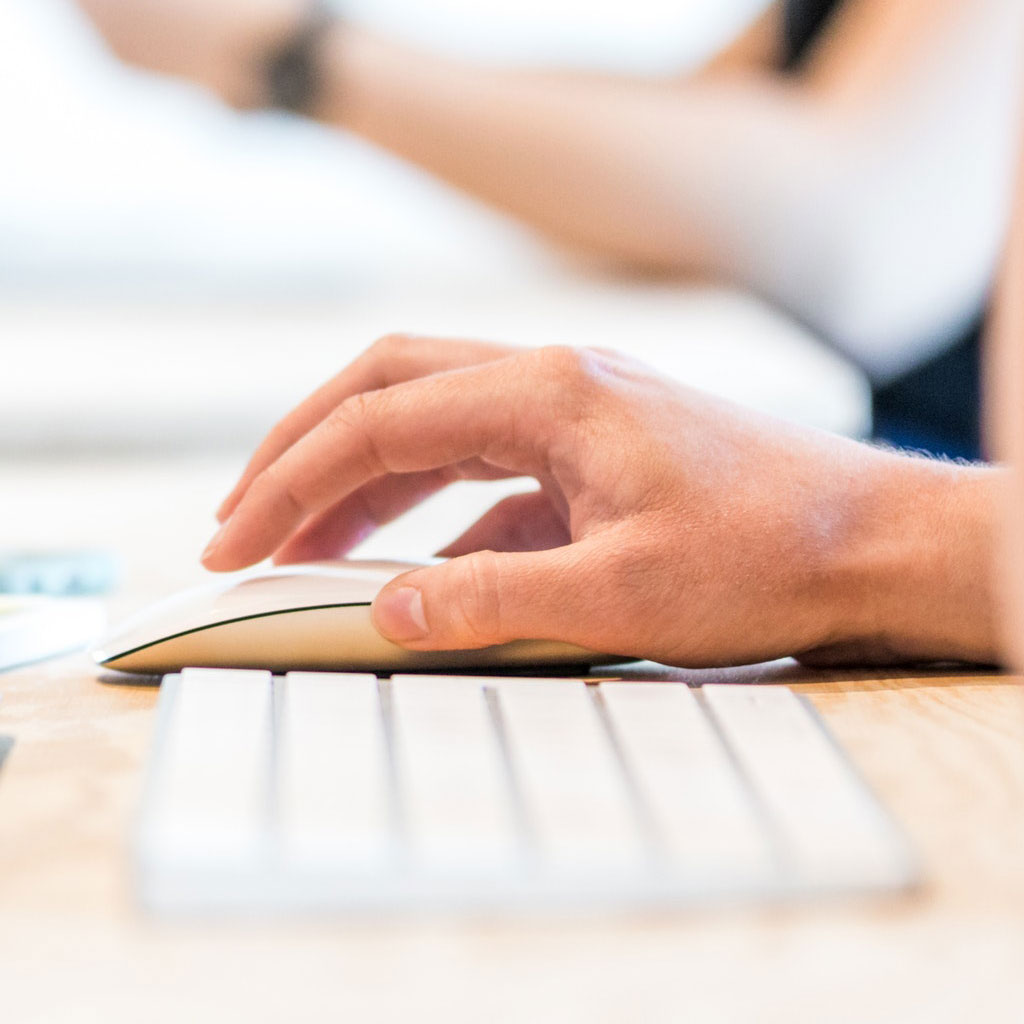
Rapid Upper Limb Assessment (RULA)
The Rapid Upper Limb Assessment (RULA) is a diagnostic tool that evaluates the required biomechanical and body posture as well as force, repetition, and load requirements of job tasks and demands on the neck, trunk, and upper extremities.
- Arms
- Wrists
- Neck
- Trunk
Your evaluation will consist of a single score that represents the MSD risk for each part of the body.
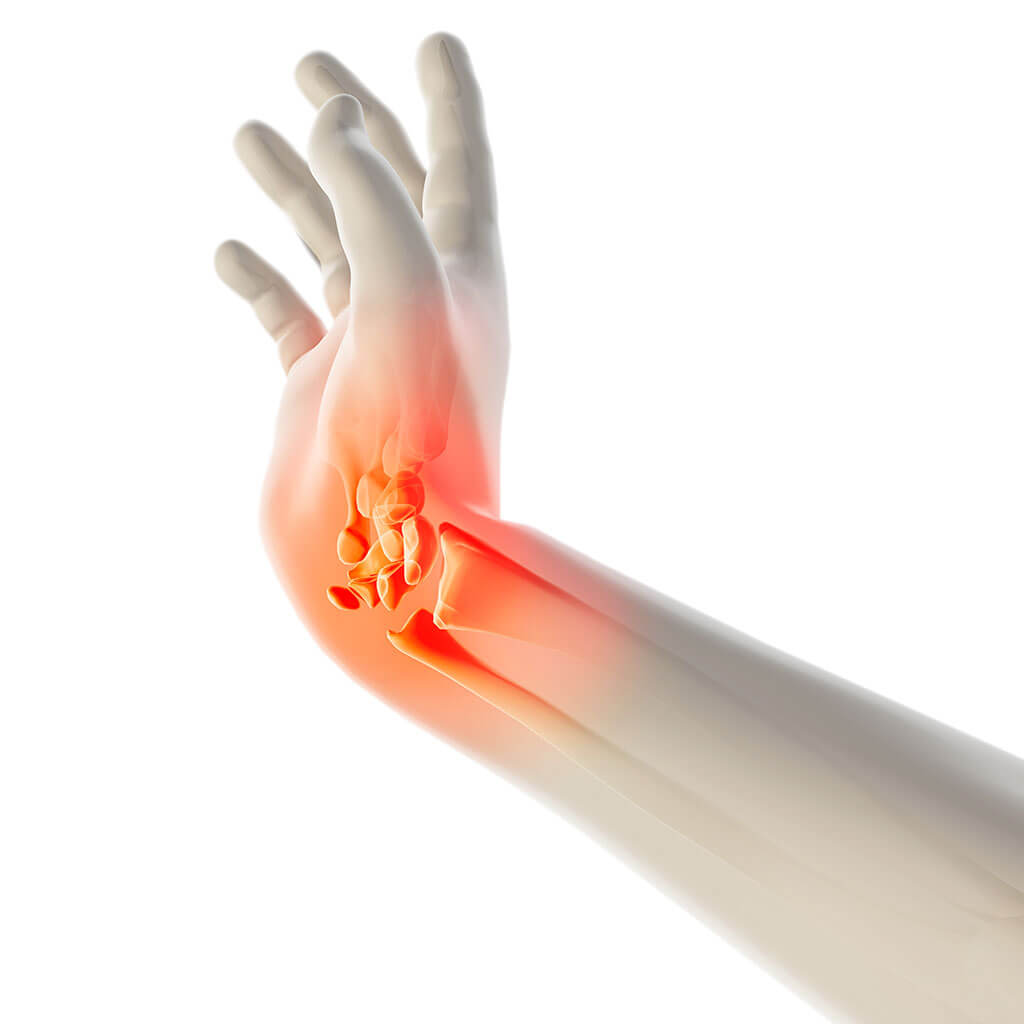
TLV Hand Activity
The American Conference of Governmental Industrial Hygienists (ACGIH) Worldwide Threshold Limit Value (TLV) for hand activity evaluates the average hand activity as compared with maximum hand force. This assessment is especially important when considering MSD and other disorders affecting the body’s upper extremities.
Symptoms and behaviors are examined among workers in relation to their TLV to determine the risk of several MSDs in the hands, wrists, fingers, elbows, and forearm.
- Carpal tunnel syndrome
- Tendonitis
- Other MSDs
Your report will define the acceptable levels of hand activity to ensure that workers can function without pain or discomfort during and as a result of their daily activities. This is especially important when considering injured employees that undergo rehabilitation and can return to productive work.

Vibration Risk Assessment
A Vibration Risk Assessment determines exposure of employees to regular, frequent, occasional or periodic vibrations. The assessment results will designate the necessary types of precautions to ensure employee health and safety when they are exposed to vibration within their job function. As with any review, we recommend that you reassess regularly (about every two years) in order to control vibration risks to your employees.
Ensure Your Employees Work Safely with a Workplace Ergonomics Analysis.
Call McClure Ergonomics Today at 336.601.0007!